Storage and Operations Improvements in Existing DCs and Infrastructure
- Alternative Storage Method
Situation:
Heavy metallic components and sheet metal panels were stored in large corrugated cases on storage racks, as received from the supplier, in active and reserve locations. Each time any SKU had to be picked or binned or replenished, these cases had to be brought down to floor, worked upon and then replaced on their rack positions . But often wasteful handling of cases was resulting as fill factor within each case was visible only after it was physically brought down to the floor, opened and checked.
Benefits Delivered:
- Fill factor was easily visible even without the need for physically handling them
- Wasteful operations got totally eliminated so as to facilitate more focus on productivity improvements
- MHEs and resources got freed up for supporting other activities
- Overall productivity of this storage zone increased by 30% on completion of this project
- Cost of DC supplies and consumables got reduced drastically
- Sustainability, reuse and recycling concepts introduced in all DC operations
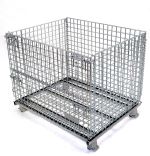
Storage and Operations Improvements in Existing DC and Infrastructure
- Alternative Storage Area
Situation:
Bulk storage for most high volume SKUs was predominantly on floor level stacking with corrugated carton cases. Some of these cases, often the ones at lower positions, were getting crushed due to the stack weight, causing collapsing of the entire stacks. This resulted in frequent wasteful re-handling, packing and re-stacking, leaving behind damages and product losses. Storage density could not be increased beyond a level as required due to this case stacking limitations.
Benefits Delivered:
- Positive and flexible bulk storage method adopted for each SKU
- Floor area compressed as stack heights could be increased even up to six high block storage
- Wastages got eliminated through damage reduction and avoidance of multiple re-handlings
- Replenishment to active and reserve storages made easy and direct from bulk stock locations
- Inventory accuracy and speed of verification made possible, all through these processes
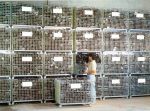
Storage and Operations Improvements in Existing DC and Infrastructure
- Creation of New Storage Zone
Situation:
Storage of Key SKUs with high handling volumes and velocities were scattered all over the storage areas. Handling and storage methods were found inadequate for dealing with them. Manual put away and picking operations were inefficient and cumbersome and hence returning low levels of productivity, quantity errors, inventory variances and longer processing time for order completion and fulfillment.
Benefits:
- Productivity enhancement achieved by over 200% for key SKUs, rendering rapid rates of put away, picking and order fulfillment
- Inventory accuracy enhanced through elimination of processing errors and avoidance of multiple touches
- Less physical strain for Floor Associates due to mechanized handling
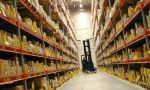
Storage and Operations Improvements in Existing DC and Infrastructure
- Storage Improvement for Fragile Items
Situation:
Storage and handling of Windshield Glasses was always a challenging affair, frequently resulting in damages, customer dissatisfaction and business losses.
Benefits Delivered:
- Damage reduction and loss prevention for this group of products
- Enhancement of service levels and improved levels of customer satisfaction
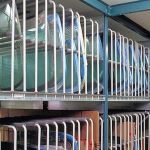
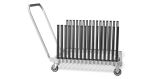